Constructions (eng)
Sound Board (Top)
Like other instruments, sound board of a guitar is the most important part which transforms vibration of a string into sound. Spruce, Western red cedar and etc. are used for the materials of wood and they are used after 5~35 years of air-dry. (From AAA class to Master class)
A. Kind of wood used in a sound board
① European Spruce (botanical name – picea abies)
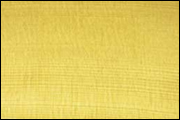
It is traditionally widely used as a sound board of a string instrument. It is distributed in Alps forests and 40 degree~50 degree north latitude forests in Eastern Europe. However, overcut of this species causes lack of supply. It is also called German Spruce as is supplied form Germany where most wholesale markets reside.
② Western Red Cedar (name – Thuja plicata)
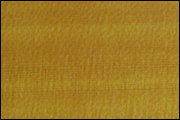
This wood has been widely used as the new material for diaphragm since Jose Ramires used and this is mass-produced around the Rocky mountains. Advantages of this species are that it is resistant to humidity, and it is easy to make a sound of a guitar with it.
③ Engelmann Spruce (botanical name – picea engelmannii)
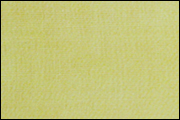
It grows naturally in the central part of Rocky mountains to the forests around the Canadian border. It is hard to distinguish this from European Spruce as they are very similar to each other. It is rather brighter, lighter, and smoother than the European and the color of the annual ring is lighter. It is mostly used as a substitute of European Spruce.
④ Sitka Spruce (name Picea sitchensis)
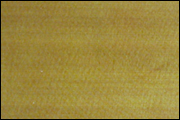
It is widely distributed around the Pacific coast in southern Alaska. It is rarely used for classic guitars except for the American artisan, John Gilbert. It is rather used a lot for folk guitars (for which steel wires are used) due to its rigid quality.
B. Selecting the top
① A plan design is decided according to musical balance of a player. (Robert Ruck, Daniel Friederick, Rafael Marodones, Rolf Eichinger, Manuel Velasquez, Robert Bouchet System, John Gilbert(With an exception of a seatcar) possible)
≦ Models in process of tests – Lattice Brace System, John Gilber-Sikta of Smallman
≦ Models without any plan – Rischuneider, J.Ramirez, P.Bernabe
Back & Side
A back of an instrument is the second significant part with side of an instrument which takes vibration of a sound board and let it resonate. Because it has to repulse and reflect sound wave generated from diaphragm, very heavy and rigidly wood is used. The species used for this are very various. Below are the examples.
1. Brazilian Rosewood (botanical name – Dalbergia Nigra)
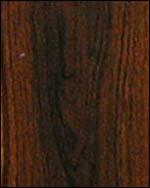
It is called ‘Jacaranda’ and it is also called ‘Bahia Rosewood’ for it only inhabits in Bahia region among the whole Brazilian forests. It is adamant, beautiful, and fragrant. It is the best class for material. However, after the Rio Declaration on Environment Development in 1992, it is traded at a pretty high price due to felling embargo, sales embargo, overseas carrying out embargo, etc which make it difficult to get the good quality of wood. The greatest possible care is needed for it is sensitive to humidity.
2. Indian Rosewood (name – Dalbergia lattifolia)
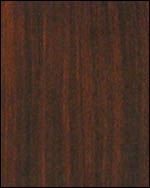
It is the most widely used species at present. Indian is known as the best and Indonesian is called ‘Sanokeling’ which is inferior in solidity and has a wide annual ring.
3. Maple (botanical name – Acer Campestre)
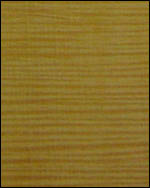
This is the species used for a bowing instrument such as a violin, a cello and etc., but as it is considerably beautiful and light, sound of a guitar is pretty vivacious tone. On account of the extremely unique sound characteristic, it is only used for extraordinary cases.
Bridge
It plays a role delivering the vibration generated from a string to a soundboard. It is divided into parts which are a part tying a string, a groove which upholds a string and a wing. It is made of rigid wood like the one used in making back and side because a great force of about 45kg is acted upon. Usually, head, bridge, back and side are consisted of the same wood to make a same design and color match.
Recently, 12-hole-bridge is developed and made. The first advantage of this bridge is that the sharped angle which is laid across saddle is manifest which makes it efficient to deliver vibration to sound board. The second advantage is that it is capable to make a neat and tidy finish. I use this method to a standard model applying positively.
Saddle, Nut
A part which sustains a string on soundboard side is called ‘Saddle’, on neck side called ‘Nut’. They are usually made of Ivory or bone etc. due to their colors which does not change after a long time. However Ivory became a item on the contraband list on account of the policy to protect elephants and because of this they generally use bone. Corian is also used and for low-grade instruments, tempered plastic called ‘Micarta’ is used.
Lining(Kerfed, Solid)
This is band-shaped wood attached to inside margin of side. This is the part which enhances durability increasing the gluing surfaces of top and back and where fan brace is fixed. Sound board part is processed curvedly sawing regularly(Kerfed) and back part is used curving Mahogany or Walnut as it is.
Fan Brace
It plays an important organizational role scattering tension of a string to the whole sound board and more important thing is top is diaphragm.
Deciding kind of wood, number, shape, width, height, length, and distance of fan brace is so important as it affects greatly on sound of an instrument and this is the part which so many luthiers in the world have been studying over several decades.
It is not too much to say that the history of development of a guitar equals to innovations of fan strut’s design. Progressive study is still made on this part but it doesn’t seem that the study will be at an end.
A guitar is an instruments which is still evolving(?) even now. Master luthiers in the world are getting outstanding results depending on their own designs and the fact that there are no same designs indicates characteristics and musical balance of players are so diverse. I make instruments with some models as standards which have been successful so far.
1. Daniel Friedrich – France(1932): Full and affluent. Has very warm and fundamental tone.
2. Robert Ruck – the United States of America(1945): Powerful and romantic tone
3. Rafhael Mardones – Chile: Due to its wide dynamic range, power of expression is so good. Makes quite stable tone.
4. John Gilbert – the United States of America(1922): Polished high tone and bass richness are the highlight.
5. Robert Bouchet – France(1898 ~ 1986): Has clear and rich timbre
Rosette
This is the part decorated with beautiful figures around a sound hole. Rosette decorates an instrument as well as prevents cracking around a sound hole. It came to be called Rose to Rosette, a very romantic name, because from old times it has been made as mosaic of a piece of wood with figures similar to a rose.
It is the only part which every luthier can express his or her artistic value and each master luthier uses his or her own design made by him or herself.
In general, they use made to order from a production-enterprise which manufactures Rosette professionally and in my case, I make according to a client’s taste.
1. 42-piece material wood inlaid mosaic (use Rosewood, Maple, Zebrawood)
2. 28-piece material wood inlaid mosaic (Rosewood, Zebrawood)
3. Rose & Spider archetype mosaic
4. 28-piece material wood inlaid original form mosaic (Rosewood, Chinese oak)
5. Other option
Neck
Wood used in Neck should be relatively light and hard so Honduras, Mahogany or Spanish Cedar is used. This method has come into wide use since Ebony was inserted in the middle of Neck for its reinforcement and Durallumin (high intensity but very light) used for material of a body of an airplane is sometimes inserted into the inside of Neck.
Finger Board
Wood used in Fingerboard is Ebony. It is distributed in the tropics such as India, Western Africa. and etc. It is very strong and heavy. The entirely black one is considered as the best and based on 12 cromatic scale, an interval of an octave is divided into 12 and Fret is fixed. By a proportional invariable(k=17.817) and by an average ratio system of measuring, an interval of sound is decided. There is also a way of determining the interval of sound by a using a divider.
In my case, regardless of any scale length, I make according to a client’s intention.
Fret
Fret is the characteristic of a guitar which can not be found in any other string instruments. By determining a position of a tone, it makes the player perform chords comfortably using left hand’s Barre. Also, string action not being interrupted by left hand fingers, it is capable to get loud volume. However, it is difficult to get a correct note and to make a differential note which decides the limitation of expression. These merits and demerits define the possibility and the limitation of guitar music.
Tuning Machine
Tuning machine has to be a product processed precisely for a smooth note control. Quality of domestic products got better but unfortunately, it is not adopted yet. I expect a tuning machine and a string with high quality which do not lag behind those of advanced countries.
David Rodgers (1.2 million won – the United Kingdoms), Irving Sloane(300 thousand won -the United States of America), John Gilbert (700 thousand won -the United States of America), Gottoh (30 thousand ~350 thousand won – Japan), Scheller (3 thousand ~ 6 thousand won -Germany) and etc.
David Rodgers makes to order and a client will get an instrument after about four months. Reference: A flamingo guitar is made of light materials such as Cypress and a mechanical tuning machine is not used because neck part is relatively heavy (The weight can be reduced by using a peg as a violin and a cello).
Heel
It is the part connecting neck and body. The curved line may resemble a line of a beautiful lady’s heel. Despite its ill- matched position, it is called ‘Heel’ and the heel is very important as a slight variation on this part makes a great move ment on neck.(The string may come off or adhere) The riskiness increases if made of a piece of wood therefore, in general, it is made jointing four or pieces of wood together. A popular model is made of a piece of wood due to its convenience. Take a look at your own instrument. If it is a real hand-made product, neck is also made by the luthier so he does not overlook this part.
Purfling & Binding
Between thin annual rings decorated on the edge of body of a guitar, the very thin wooden part on the inside is call ed ‘purfling’ and the relatively thick wooden part on the outside is called ‘Binding’. Plastic(ABS) is used for a low-class instrument and for a high-class instrument, wood which is stooped is used. As this is not the part which vibrates, it does not affect sound. However, when an instrument gets shocked, wooden material is considered more desirable to protect the instrument. (It is more elastic) Moreover, the function is keeping grain of wood from cracking when it repeats expanding and contracting.
Finish
There are several traditional ways of painting being handed down from ancient times but shellac painting developed and descended mainly in France is used a lot in instruments. Schellac, the painting made from refining specific lac-insects which secrete phlegmatic temperament and adding pine resin, is used melting in alcohol. It has been used for painting instruments for a long time as it is possible to finish very thin and in case of bowing instruments, this is the paint skill still regarded very important till now. Due to development of modern civilization, a various kinds of paints have been developed and applied to guitars and if they are largely classified, there are three types.
1. Poly-Urethane
It is easy to understand if you think it the same painting as the one used in furniture. It occupies the majority of low-class instruments but also used in exquisite instruments such as P.Bernable, M.Contrares, J.Ramires etc.
2. Nitro-Cellulose lacquer (Gloss lacquer)
This is the method many luthiers prefer as it is capable to paint very thin and also preservation and repairing are relatively easy.
3. Schellac
Though it is able to paint very thin, it is troublesome to manage. Repainting every 3~5 year is needed. It is used a lot in the highest-class instruments. Reference: Instruments with Lacquer and Schellac finish are apt to wear out and the paint may melt if Volatile spray wax or an abrasive containing silica is used. Therefore they should never be used. Reference 2: Different from other Bowing instruments, characteristic of sound pressure appears in an instant in a guitar. (Attack is quick – characteristic of string instruments) For a Bowing instrument(sort of violin) of which sound lasts continuously, painting is managed with great care because the quality of a tone changes great according to the kind or the width. However, in case of a guitar, the characteristic of timbre disappears rapidly so relatively, a lot more consequence is given to the design of diaphragm. I agree to Robert Ruck, an American master craftsman, who said, “If it is capable to paint thin, no matter what the painting is” and I would like to recommend Lacquer rather than Schellac which has many defects.
Case
There are luxurious cases as Mark leaf, SKB, Hiscox and etc. but they are so expensive. As the purpose of a case is to preserve an instrument and to intercept humidity, I would like to recommend a domestic case. (a Styrofoam case 50 thousand won~ 60 thousand won)
String
The effect of a string which affect the efficiency of an instrument is likely to excel people’s imagination. Hannabach, D’addario, Augustine, Aliiance, Aranjuez etc. are strongly recommended. Moreover I sell every single name brands according to its difference in tension such as low, medium and high tension therefore, you may choose whichever fits to your instrument.
Hygrometer
A materterial wood instrument is very sensitive to humidity. If the humidity is high, cells of wood absorb moisture and swell.(perpendicular direction to annual rings) As side fixes the shape of the instrument, it looks like the full round stomach and if excessive, it may cause irregularity. Then it may be followed by the bridge ascending and also by the height of strings ascending. After that, a great force is worked on the soundboard making the sound dull.(rainy season) In contrast, if it is too dry, the humidity of the soundboard comes off and makes it contract if it is too much. (winter time) In case of Korea, humidity changes considerably severly which makes it hard to keep an instrument in a steady humidity but neglecting this duty will let you pay dear. As for me, I make instruments under average humidity of 60% to 50%~55%. To take care of the instrument properly, a hygrometer is essential. If the humidity does not reach standard humidity, a humidifier or a Dampit (kept in the case) can be used, and if excessive, the relative humidity should be lowered by using a dehumidifier, a silica gel or an air-conditioner.